HICS™ scheme designs include all power distribution, low voltage control logic and interface terminal arrays and where required includes single, two or more safety channel logic using non generic hardware (different manufacturers), such a system would generally be required with cranes employed in handling volatile material such as in the nuclear environment and is designed to eliminate generic failure. Subject to the control mediums to be incorporated, designs can take into account for off crane ground based control methods such as remote control, control desk operations, fixed or mobile pendant operation or traditional in cab control. It is common to include a number of optional control systems for specific reasons.
Automated handling schemes and complex zone movement control plans for cranes in operationally restricted safety zones are entirely developed by HICS™ design engineers or from clients own ground operating system requirements. Where acceptable within a scheme, PLC’s are incorporated for specific logic control.
All motor control gear and connectivity hardware of HICS™ design is housed in either standard locking cubicles (enclosures) and where a suite of enclosures are built as an assembled structure, these incorporate electrical and mechanical interlock systems as a standard feature for obvious personnel safety and integrity reasons. For low headroom constraints specially constructed cubicles (complete suites) can be designed and built to suit. HICS™ can build full EMC compliant (emission leak proof) enclosures, an example is shown following for a contract that was critical to the application.
For effective motor speed control a number of scheme design options are available, these include but not limited to series resistance banks for slip-ring type electric motors like used for older convention applications, constructed using spool or grid type resistance banks, (with stainless steel options) and vermin control shields and optional ventilated methods.
Variable Frequency Drives (VFD’s), Flux Vector Drives (FVD’s) and Eddy Current Brakes (ECB’s) all options can be fully integrated with the control scheme. Generally the control choice is application or integrity dependant or both. All drive electronic drive variants have suppression and filtering.
An important part of EMC compliance is the use of screened power cable networks between electronic speed control devices and the physical electrical drive motors. Where full EMC protection is required, all external cable routes between relevant control cubicles and interconnection termination boxes exit via special stainless steel EMC compression glands. Throughout the construction phase, client representatives usual carry out build inspections at specific contract milestones.
HICS™ can also provide a full package of control equipment hardware and installation materials to comply with up to date standards, rules and regulations as laid down by the regulatory authorities, as a minimum, of the country of destination.
Depending on the contract terms and value we can provide:-
- Full dimensional mechanical layout drawings
- Automatic inter-connecting continuance page related schematic drawings
- Full test plans formulated and carried out prior to despatch
- Bills of materials detailing the installed position of the parts
- Automatic connectivity termination sequencing
- Automatic component and wire labelling
- Designed schemes (as built) downloaded to CD for client record
- Full operating and maintenance manuals.
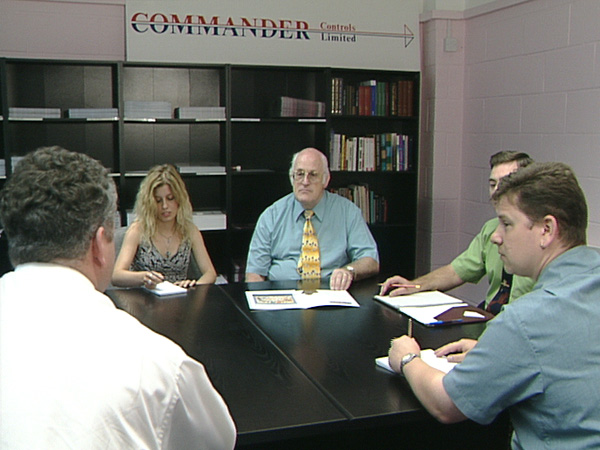
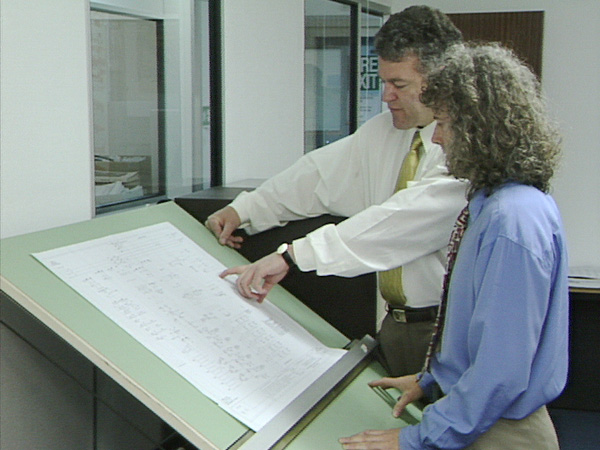
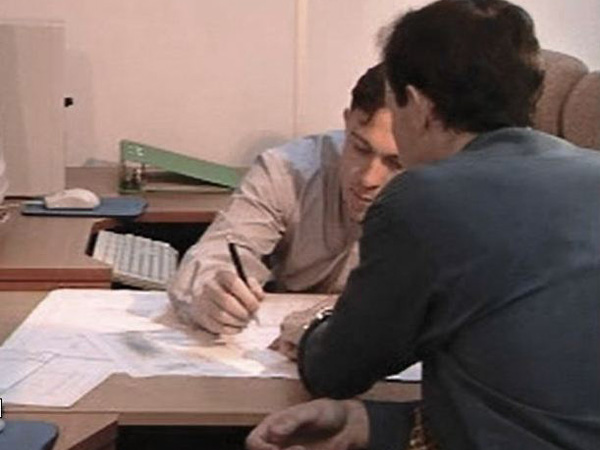
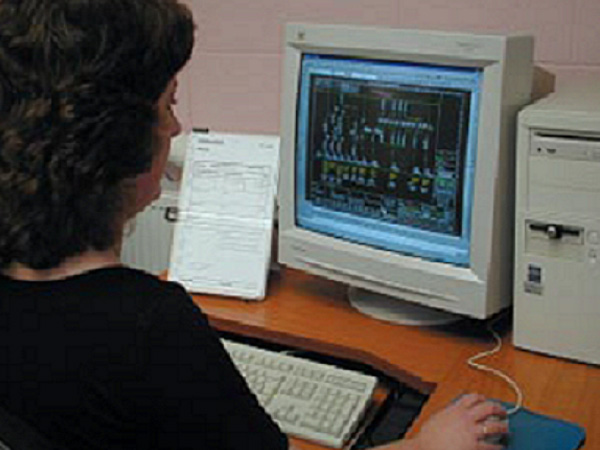
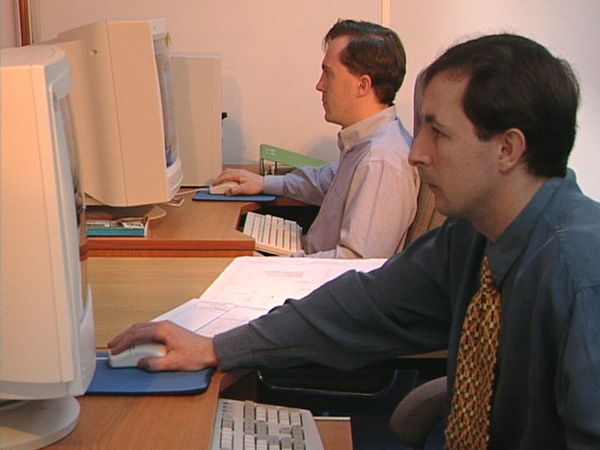
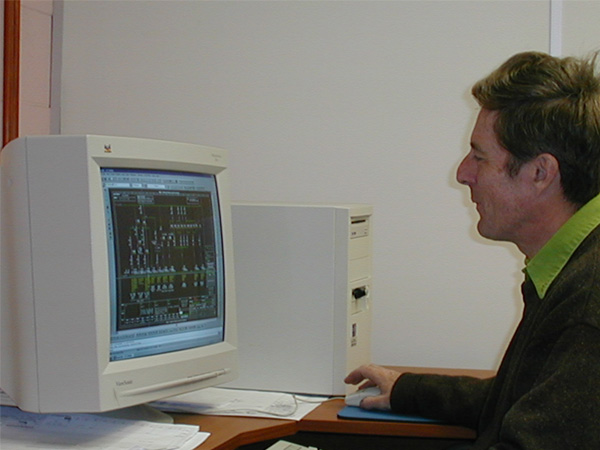
