ComDrive™ Eddy Current Brake Control & Safety System
Safety * Reliability * High Efficiency * Low Maintenance * Field Proven System
Nuclear Industry Approved * Power Generation Industry Approved
ComDrive™ machine is IP54 rated and are available in 4 sizes from 2.2kW to 150kW (optional size 5). The ComDrive™ machine is simple and reliable and is similar in construction to a squirrel cage (induction) motor, but has a DC field coil system with a solid steel balanced rotor developed for higher efficiency and reliability as opposed to types using riveted laminations in their construction (these can magnetically oscillate and fatigue, such a method reduces the machine life).
Construction
ComDrive™ Eddy Current Brake Units are constructed to a uniform footprint from high quality tested and Mill certified materials. Cooling is provided by a separately driven forced air cooling fan motor with in-built air flow sensor which is coupled into and monitored by the Prospeed-II™ Closed Loop Speed Control System. This method of cooling has considerable advantages to performance and efficiency over the entire range of ComDrive™ Machines. Cooler running means closer tolerances between the rotor and field coil pole pieces can be achieved particularly at low speeds. The monitored cooling fan assembly can be oriented during manufacture if required to suit close (low) headroom installations. One level of Thermistor protection is provided as standard to protect against temperature rise. A Metrosil™ device is incorporated to protect against field spikes. Yellow finish.
Operation
The Prospeed-II™ Closed Loop Speed Control provides a varying DC Voltage and Current to the ComDrive™ field winding producing a magnetic field between the stator and solid moving rotor. The slip ring rotor voltage from the motor is used to represent motor speed and is monitored by the Prospeed-II™ Unit to vary the applied magnetic field strength in order to achieve the desired pre-set speed. Separate contactor control of rotor resistance switching assists the motor speed torque development.
Maintenance
There is no need for carbon brush gear and very little maintenance is required other than occasional (6 monthly) greasing of rotor shaft bearings via the fitted lubrication system and replacement of the ventilation filters.
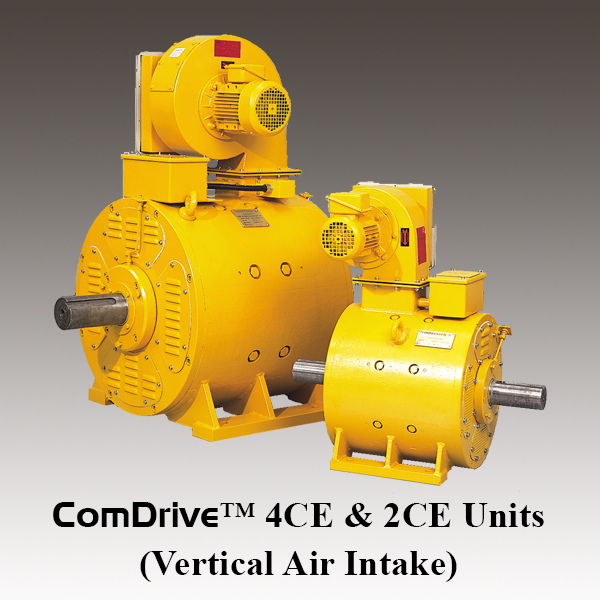
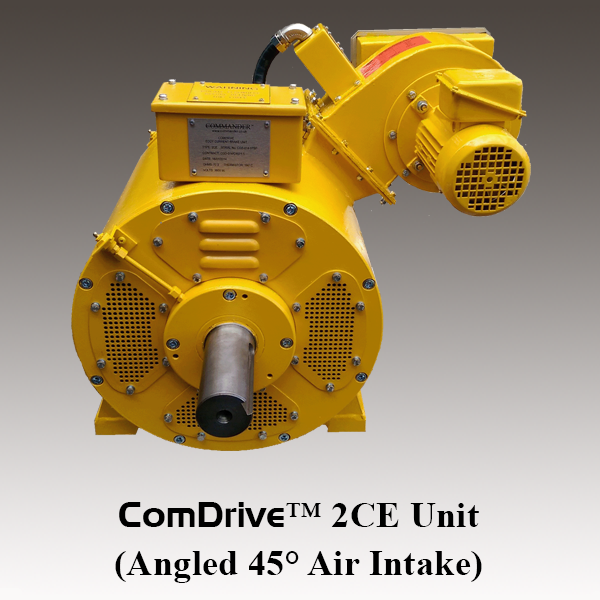
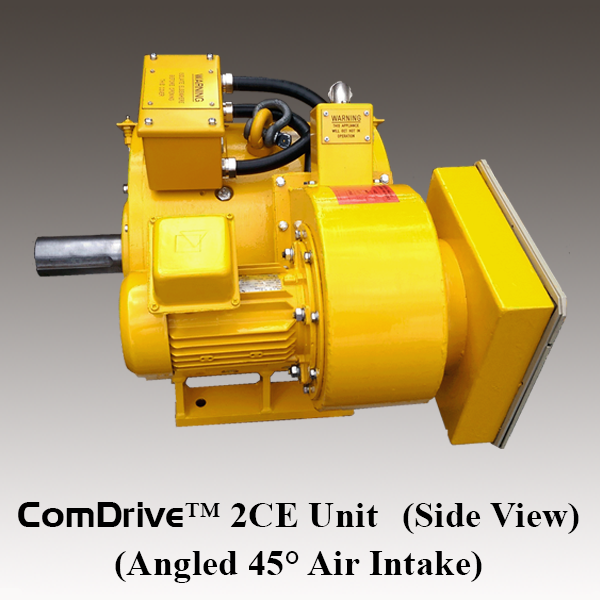