Resistance Banks for speed control can only be used on electric motors that incorporate a wound rotor, known therefore as a slip-ring motor. This type of motor has a stator which has electrical field coils wound in the structure and similar to a simple induction type motor. When energised an electromagnetic field is created and thus causes the rotor to excite and rotate in a given direction (this is determined by electrical phase rotation) exactly as an induction motor. Reversal of motor direction is as with the induction type motor, reversal of two phases to the stator connections.
The slip-ring type motor incorporates a rotor that also has electrical windings (coils) embodied therein, these are connected to a slip-ring assembly with brush gear thus to provide a connectivity method for external resistance bank connections.
Resistance Banks are divided into sections to suit the motor characteristics and numbers of speed stages required. The more resistance stages the wider range of speed control is available. Each resistance section is switched out across three poles using rotor contactors thus to permit a gradual increase of the motor speed. Not all speed settings are controlled by a ground based operator or even on-crane cab controls. Frequently timing systems are applied to automatically take the crane acceleration through the various crane speed steps thus to increase the motors rotational speed.
On start-up, full resistance is in circuit to the three rotor poles. Gradually the drive motor gradually overcomes the resistance stage enabling maximum speed for the speed step. As each resistance section closes, motor acceleration speed progresses until all resistance stages are closed, the motor then becomes direct on line permitting full speed and torque.
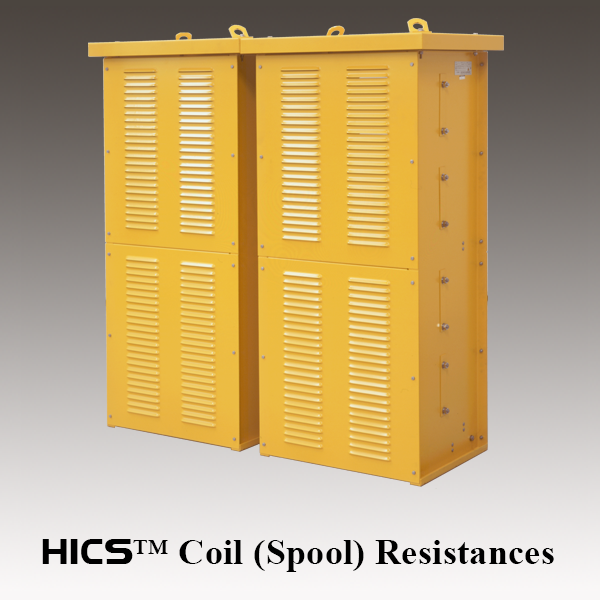
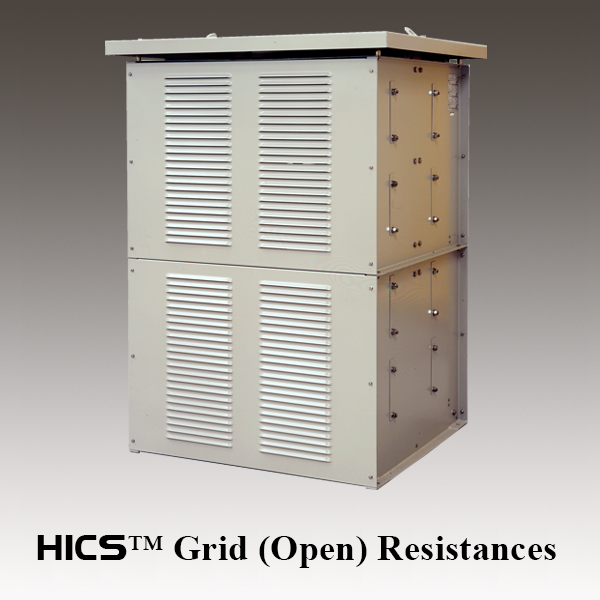
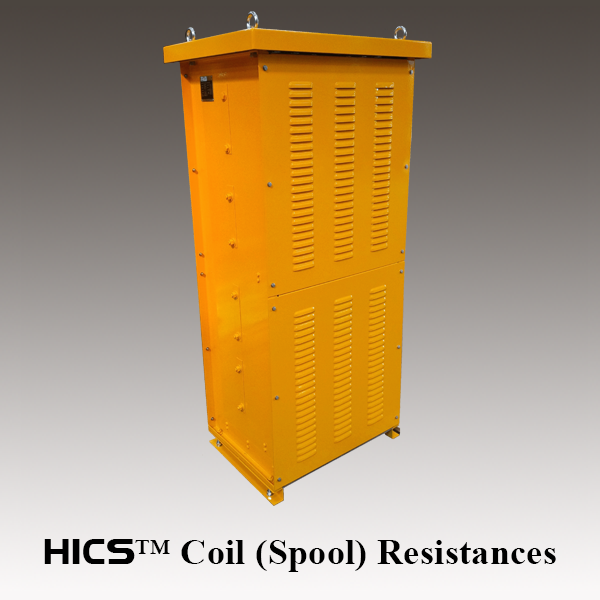
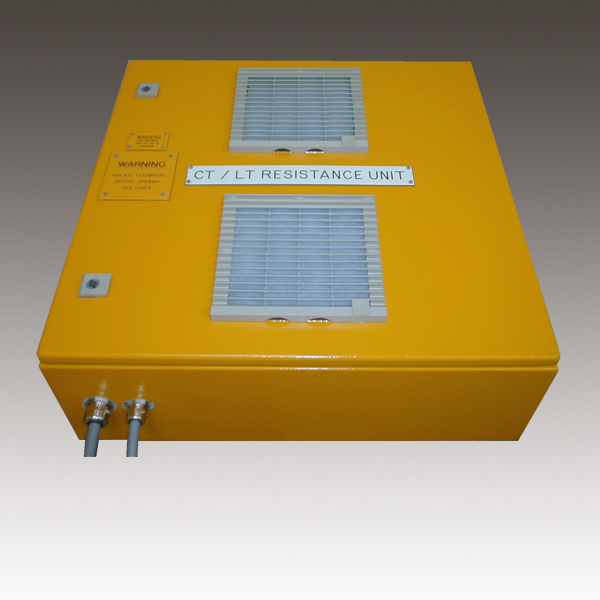